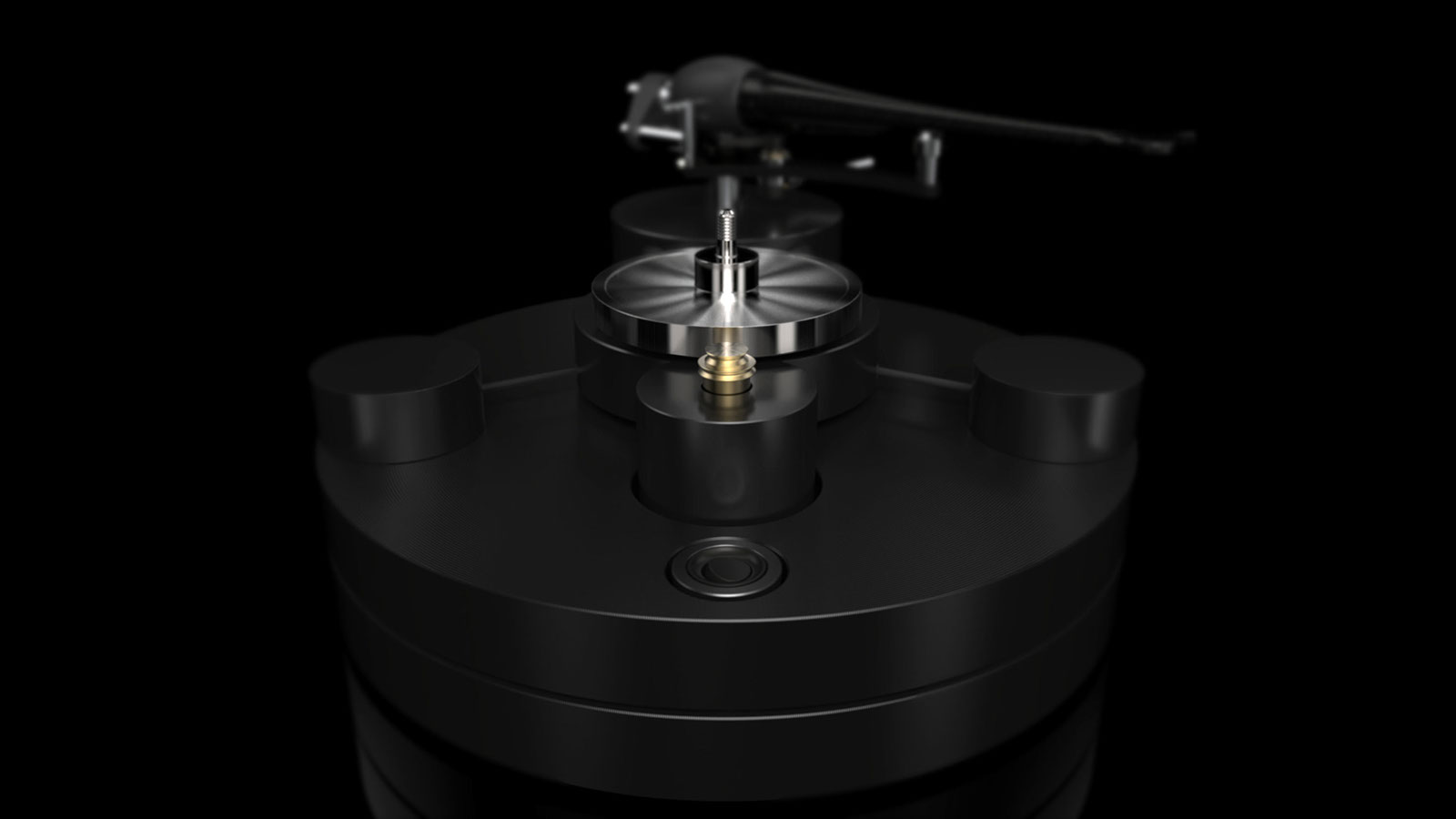
“For vinyl lovers, it’s important to know that Wilson-Benesch first began in 1989 as a start-up dedicated to building a turntable simply because it felt vinyl was a superior medium compared to CD. For that reason alone, the company should be venerated. W-B argued that new, emerging technologies like carbon fibre could further elevate vinyl playback.”
– Michael Fremer
Overview
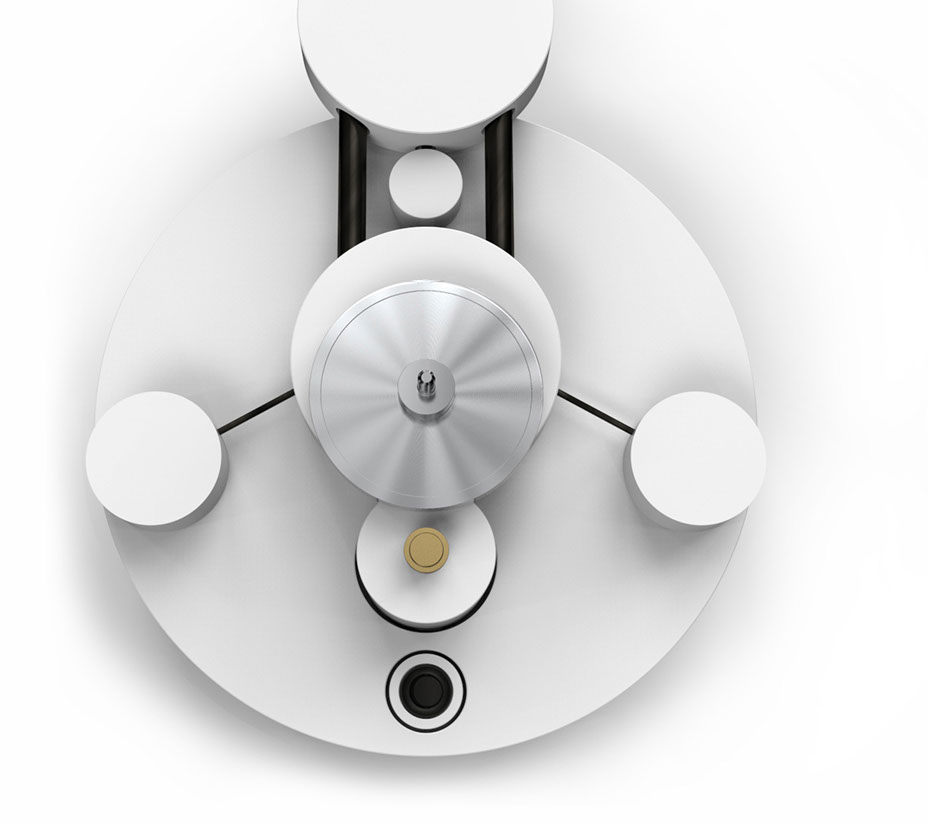
In any design, ultimate high performance can only be attained when all the components have been optimised to work in harmony. Following this philosophy Wilson Benesch have taken all design and manufacturing in house to create the Circle 25 turntable. Using State of the Art Dassault CAD/CAM Systems, Wilson Benesch precision engineer each component in the Circle 25, within a tolerance of 0.01mm, to create a perfectly engineered masterpiece.
Forming the principle structural components of the Circle 25, the distinctive two-part Polyoxymethylene (POM) circular plinths replace the MDF plinths used in the original circle design. POM is a high-grade engineering homopolymer exhibiting superior stiffness and a higher damping coefficient.
The lower plinth houses the motor assembly, which is isolated from the upper plinth by three lossy polymer nodes. In turn, the upper plinth sees three alloy nodes meet with unidirectional carbon fibre cantilevers to create a unique sub-chassis suspension. The carbon fibre cantilevers are central to the success of the Circle 25 design. They exhibit exceptional stiffness and energy damping, providing a solid reference point for the platter and damping any structural borne resonance. This highly optimised design translates directly into the sonic presentation of the Circle 25, creating a wide-open soundstage, with the ‘blackness’ and solid quality to the analogue sound.
The final element is the bearing. The Circle 25 references the past to redefine the future. Taking elements of the original bearing design, the new bearing combines a hardened steel shaft and captive ball bearing, with a phosphor bronze bearing hub. With a highly polished surface finish, the bearing ensures the lowest possible level of friction and noise, while being phenomenally resistant to wear.
A turntable is purely a system of measurement, designed to allow a ~10nm (0.000001mm) cantilever tip to trace a ~50µm (0.05mm) groove in a piece of vinyl. By considering the microscopic level, it is then easy to appreciate the beauty of the Circle 25 design. What appears a simple design is in fact a complex and highly engineered analogue replay system.
Technology
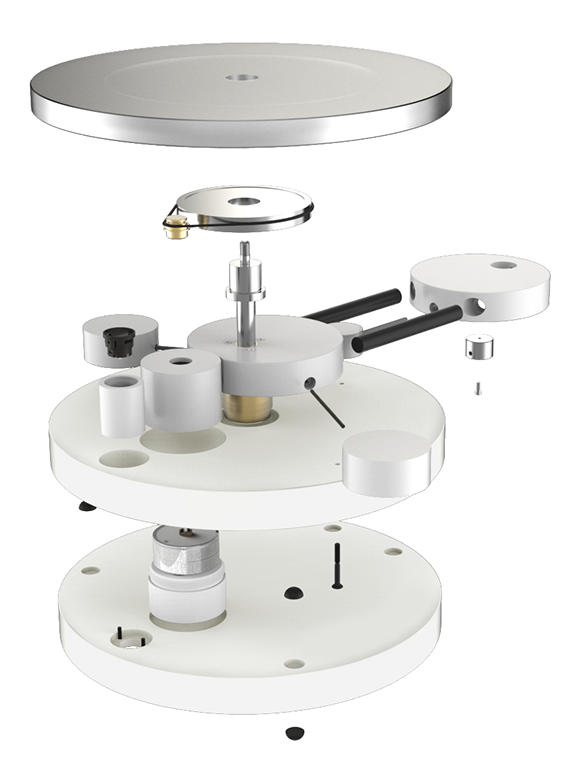
ACRYLIC PLATTER
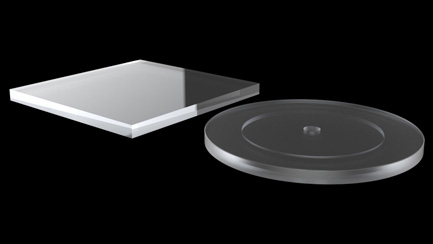
The Circle 25 is supplied with a precision-machined acrylic platter that has been turned in house at Wilson Benesch. This critical component must be machined perfectly to ensure that the vinyl on the platter spins true.
OPTIMISED BEARING
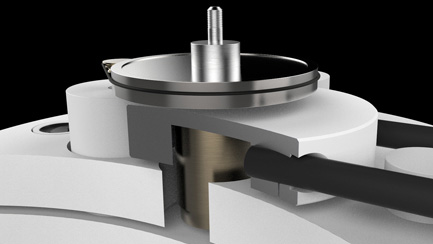
The Circle 25 bearing is a highly engineered, precision-machined set of components produced from phosphor bronze and hardened steel.
The steel sub-platter meets with a hardened steel shaft, which in turn holds captive, a hardened steel ball bearing in the base of the bearing hub. The bearing hub is machined from phosphor bronze, which comprises the shaft and the end cap. These two elements form the critical meeting point with the captive hardened steel ball bearing. Highly polished and resistant to wear, these components legislate for the lowest level of friction and noise within the bearing.
Machined and finished in house, every component used in the Circle 25 bearing has been manufactured to exacting tolerances, guaranteeing the bearing at the heart of the Circle 25 is perfectly aligned and accurate.
CANTILEVER CARBON FIBRE SUSPENSION
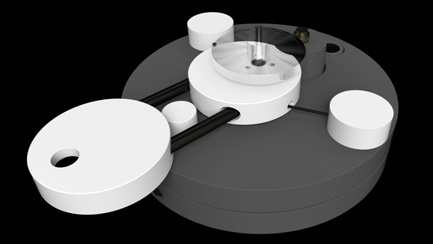
The immensely stiff carbon fibre cantilevers in the Circle 25 act like springs, damping energy as a result of their high longitudinal specific stiffness.
The Circle 25 uses two different diameter carbon cantilevers in the design; Three smaller 3.7mm diameter cantilevers isolate the bearing hub from the upper POM plinth via the three aluminium hubs, while two larger 12.3mm diameter cantilevers isolate the arm hub from the bearing hub.
The large diameter cantilevers provide very high specific stiffness, ensuring maximum stability in the arm hub. The smaller diameter cantilevers have a lower specific stiffness, allowing for more energy damping.
The carbon fibre cantilever suspension system is a highly tuned and unique approach to turntable suspension design.
TWO-PART CHASSIS CONSTRUCTION
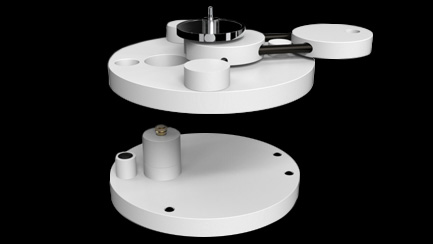
The Circle 25 uses a two-part platter construction. This allows the motor and power supply to be built into the lower plinth, with the three alloy suspension hubs, the arm and bearing hub built onto on the second plinth. Any noise from the motor and power supply is therefore isolated from the second plinth in part by the two-part construction, but also by the three sorbithane nodes which act as the mechanical link between the upper and lower plinth.
POLYOXYMETHYLENE CHASSIS
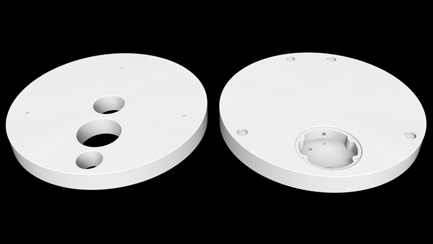
Polyoxymethylene (POM) is a high-grade engineering polymer that exhibits superior stiffness and damping properties versus the MDF used in the original design. In addition, POM is a more dense material, with a higher mass making the Circle 25 3kg heavier than the original design. With this additional mass at the base of the turntable, the overall stability and energy damping of the Circle 25 is vastly improved.
Another advantage of POM is its excellent machinability. You would never construct a turntable from solid aluminium, owing to the fact the material would resonate and damp structural borne energy poorly. However, POM has a material hardness akin to aluminium, but exhibits excellent damping properties. This allows Wilson Benesch to bring manufacturing of the Circle 25’s two POM plinths entirely in house. Both machining and finishing is done in one process, allowing a high precision component to be realised with a beautiful machined finishing as seen in the Wilson Benesch R1 HiFi Rack.
Explore the Circle 25
Review / Award
Technical Details /// Circle 25
Designs
Advanced materials used throughout.
Totally unique design concept.
Low mass design.
Immensely stiff unidirectional carbon fibre rods used in the principle structural components.
High tolerance phosphor bronze plain bearing with tool steel spindle.
Dimensions
Diameter: 305mm (12″)
Stacked Height: 140mm (5.5″)
Weight per Channel: 4kg (9 lbs) or 8kg (18 lbs) with stand
Finishes
Machine finished polyoxymethylene plinths (black or white)
Colour coded, silk finish support hubs and casings
Machine finished translucent acrylic platter